

Armed with this knowledge, as long as boost pressure is below a predetermined allowable ceiling, the EMS will open the boost control solenoid to allow the turbocharger to create overboost beyond what the wastegate would normally allow. The basic algorithm sometimes involves the EMS (engine management system) "learning" how quickly the turbocharger can spool and how quickly the boost pressure increases. Or, by monitoring manifold pressure in a feedback loop, the engine management system can monitor the efficacy of PWM changes in the boost control solenoid bleed rate at altering boost pressure in the intake manifold, increasing or decreasing the bleed rate to target a particular maximum boost. The wastegate control solenoid can be commanded to run in a variety of frequencies in various gears, engine speeds, or according to various other factors in a deterministic open-loop mode. Solenoids may require small diameter restrictors be installed in the air control lines to limit airflow and even out the on/off nature of their operation. This effectively changes the air pressure as seen by the wastegate actuator diaphragm. This effectively alters the flow rate of air pressure through the valve, changing the rate at which air bleeds out of the T in the manifold pressure reference line to the wastegate. By varying the pulse width to the solenoid, the solenoid valve can be commanded to be open a certain percentage of the time. The boost control solenoid contains a needle valve that can open and close very quickly. In effect, a boost-control solenoid valve lies to the wastegate under the engine control unit´s (ECU) control.

For this reason, systems that do not feature closed loop operation are not as widespread.īoost controllers often use pulse width modulation (PWM) techniques to bleed off boost pressure on its way to the reference port on the wastegate actuator diaphragm in order to (on occasion ) under report boost pressure in such a way that the wastegate permits a turbocharger to build more boost pressure in the intake than it normally could. Since open loop systems do not modify control levels based on MAP sensor, differing boost pressure levels may be reached based on outside variables such as weather conditions or engine coolant temperature. Open loop specifically leaves out a desired boost level, while closed loop attempts to target a specific level of boost pressure. Open loop systems have a predetermined control output where control output is merely based on other inputs such as throttle angle and/or engine RPM. Closed loop systems rely on feedback from a manifold pressure sensor to meet a predetermined boost pressure. On a blocking configuration, air traveling from the charge air supply to the wastegate actuator is blocked while simultaneously bleeding any pressure that has previously built up at the wastegate actuator.Ī 4-port pneumatic solenoid installed to control a dual port wastegate controlled by a single PWM PID controllerĬontrol for the solenoids and stepper motors can be either closed loop or open loop. In a bleed-type system air is allowed to pass out of the control lines, reducing the load on the wastegate actuator. Either can achieve the goal of reducing pressure pushing against the wastegate.
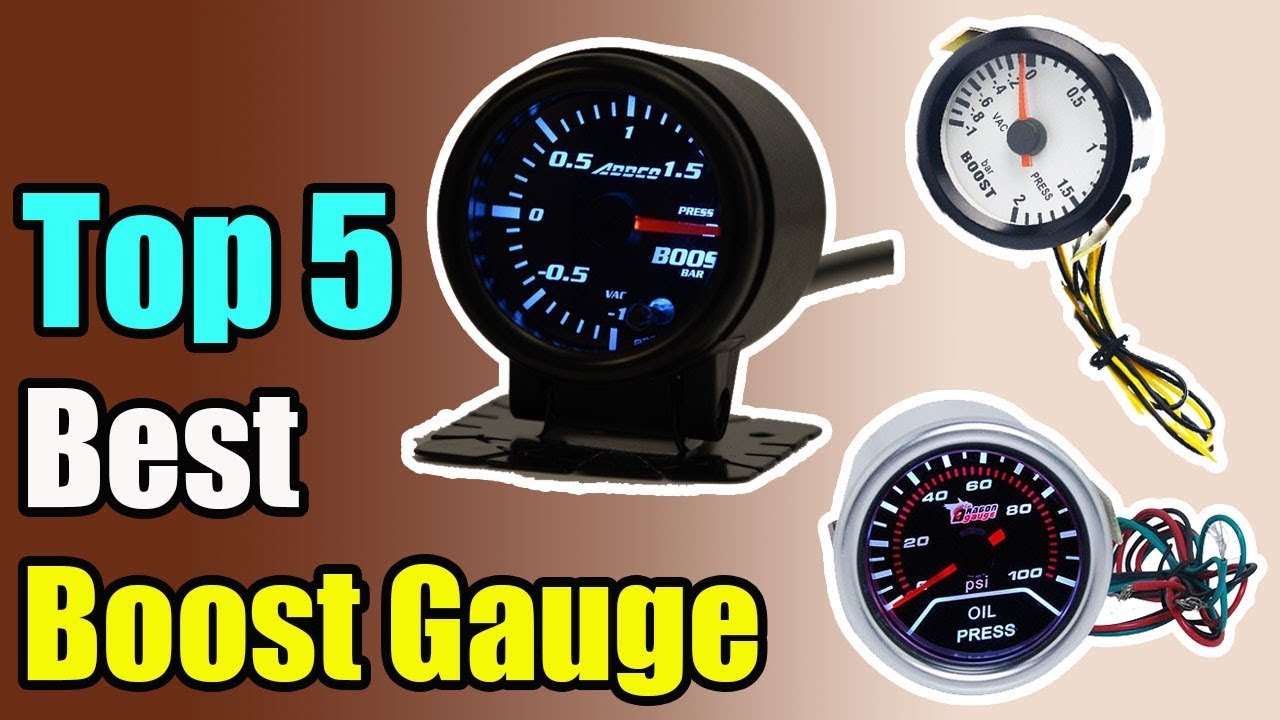
Further control and intelligent algorithms can be introduced, refining and increasing control over actual boost pressure delivered to the engine.Īt the component level, boost pressure can either be bled out of the control lines or blocked outright.
#What is the best boost gauge manual#
The same general principle of a manual controller is present, which is to control the air pressure presented to the wastegate actuator. This solenoid allows interrupt or blocking of the boost pressure rather than just bleed type control.Įlectronic boost control adds an air control solenoid and/or a stepper motor controlled by an electronic control unit.
